半導体業界のパーティクルの計測方法一覧
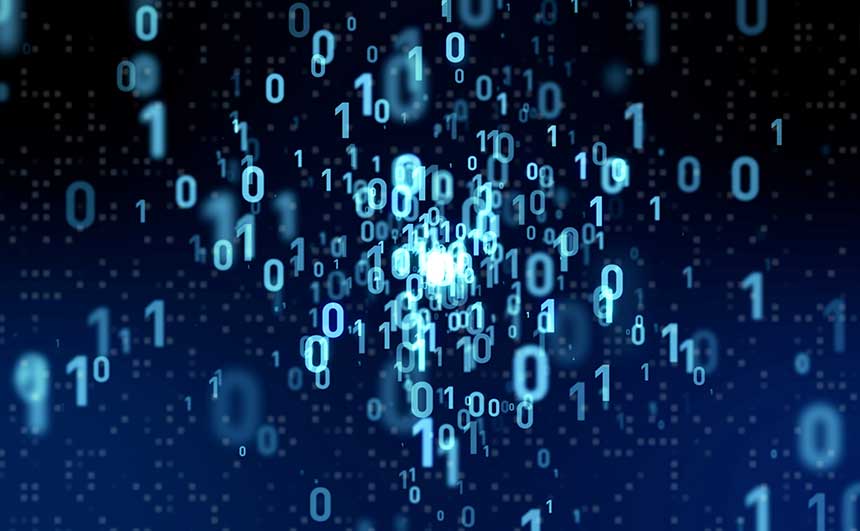
半導体製造プロセスにおいてパーティクル(微粒子)は大敵です。
ウェーハへのパーティクル付着は製品の不良を生じさせるため洗浄装置で取り除かれます。
しかし洗浄後の搬送時や各プロセスの装置内にてパーティクルが付着する場合もあります。
装置内の反応により光学系がパーティクルにより汚染されるケースなど、ウェーハ以外にも悪影響を及ぼすこともあります。
そこで、製造装置内や、ウェーハ表面、レチクル、ペリクル等にパーティクルがどの程度存在しているのかについて、計測・カウントする方法と原理をまとめてみました。
パーティクル計測方法
パーティクルの計測方法について、走査電子顕微鏡(SEM)による分析や凝縮粒子カウンターから、最新の画期的な方法まで6つご紹介いたします。
SEM
走査電子顕微鏡(SEM)によりパーティクル計測が行われています。
しかしSEMの役割は気軽な計測ではなく、観察や分析に適したものと言えます。
SEMでは倍率を設定してSEM像を撮像し、その画像を見ながらパーティクルを観察しますが、何の前情報もなしにSEMのみでパーティクルを発見するのは非常に根気のいる作業です。
パーティクルの検出のためには高倍率でSEM像を取得する必要がありますが、視野は狭くなります。
ウェーハとパーティクルはしばしば野球場と砂粒に例えられますが、実際に視野が狭められた状態でパーティクルを探すのは、さながら野球場を歩いて砂粒を見つけ出すような、忍耐を要する作業でしょう。
そのため「パーティクルの位置情報の特定」が可能な方法、例えばSEMに暗視野光学顕微鏡を搭載するというような方法が用いられています。
暗視野光学顕微鏡によってパーティクルの散乱光を検出しすることで、パーティクルの位置をある程度まで絞り込み、SEMではその位置情報をもとにパーティクルを撮像するといった手法です。
電子線を照射し表面を観察するSEMは、光学顕微鏡ではわからない微細な形状も判別できるため、ウェーハ上に付着したパーティクルの形状の観察に役立ちます。
またSEMは、エネルギー分散型蛍光X線分析など、別の技術と併用することで、不着物質の分析や同定が可能になり、パーティクルの発生源の特定や、汚染の原因究明に貢献するものと言えます。
表面検査装置(欠陥検査装置)
ウェーハ表面の欠陥やパーティクルの検出に用いられます。
ウェーハ表面へレーザーを照射しレーザー散乱光の観測を行ないます。
高額であること、ウェーハ表面にしか対応していない等制約が多く、汎用的な付着パーティクル計測に用いることはできません。
パーティクルカウンター(微粒子計測器)
パーティクルカウンターとは、気中(空気中)や液体などに存在する微粒子(パーティクル)の数を測定する機械です。
半導体業界で用いられる2つのパーティクルカウンターについてご説明いたします。
凝縮パーティクルカウンター(CPC)
凝縮パーティクルカウンターは凝縮核法を応用した装置で、気体中に浮遊する微小なパーティクルをアルコールや水を用いた過飽和蒸気によって成長させ、粒子を検出します。
凝縮核計数器とも呼ばれ、CNC(Condensation Nucleus Counter)やCPC(Condensation Particle Counter)といった略語で記載されることもあります。
凝縮パーティクルカウンターの機器内部では、あらかじめアルコールや水を加熱と冷却を通じて過飽和状態にしておきます。(過飽和状態を作り出す方法には断熱膨張や伝導冷却といった方法がありますが、まずはパーティクルを流す過飽和ガスを生成します。)
過飽和ガスへと微粒子を通すことで、過飽和ガスが飽和状態に変化する際に、微粒子が凝縮成長するため、これを検出します。
気中パーティクルカウンター(クリーンルーム用)
気中パーティクルカウンターは、クリーンルームの空気中に浮遊するパーティクルを測定する機器で、その測定には凝縮パーティクルカウンターと同じく、光散乱の原理が用いられます。
測定方法はシンプルで、まずは測定空間の空気を装置内部に吸引し、レーザーが照射される位置まで誘導します。
吸引された空気にレーザーを照射し、パーティクルの散乱光をフォトダイオードで受けて、電気信号へと変換します。
散乱光強度によって粒径を求め、電気信号の数に応じて粒子数を判断できます。
クリーンルームの空気清浄度は国際規格(ISO14644-1)に基づいて評価されますが、気中パーティクルカウンターの場合、リアルタイムで粒径や粒子数をモニタリングできるため、クリーンルームのパーティクル管理に有効です。
しかし対象は気中に限定されるため、例えば装置内の付着パーティクルの計測のような用途には適しません。
UV光源を用いた検査装置
半導体検査装置にはUV光源が用いられ、ウェーハの付着物や汚染を見極める表面検査や外観検査に有効です。
DUV(深紫外線)を用いているものが多くありますが、極端紫外線(EUV:Extreme Ultraviolet)を用いた検査装置も登場しています。
それらは高性能ですが当然ながら高価なものです。
表面付着パーティクル測定装置
これまでご紹介したパーティクル計測は、製造装置内に生じるパーティクルを「手軽に」「時間を掛けずに」「比較的安価な設備で」「高品質に」計測することが困難でした。
それを解決した最新のパーティクル計測ソリューションが表面付着パーティクル測定装置であるFastmicroです。
実は、パーティクルは気中に浮遊しているものに限らず、装置内や搬送経路等に付着した状態にあり、それが落下・浮遊して生じることがわかっています。
Fastmicroはその付着した状態のパーティクルを、装置奥などの採取しにくい箇所でも容易に採取できる、新しくかつ効率的なツールです。
コスト面も従来の方法に比べメリットがあります。
Fastmicroは、EUV露光装置を世界で唯一製品化できているASML社のパーティクル低減プロジェクトで生まれ、活用されている画期的な製品です。
半導体業界において今ホットな分野のひとつとして、13.5nmの波長を用いたEUV露光装置による最先端の微細プロセスがあります。
ASML社がEUV露光装置を製品として実現する上で、パーティクルの低減がどうしても必要でした。
そこでASML社の部品供給パートナーネットワークに導入し、見事成果を上げたシステムがこのFastmicroです。
Fastmicroはミー散乱光を応用した効率的な独自の測定方法を持っており、半導体製造装置内部や製造プロセスのパーティクル計測に最適です。詳しくは製品ページをご覧ください。