半導体業界における発塵源の効率的な特定方法
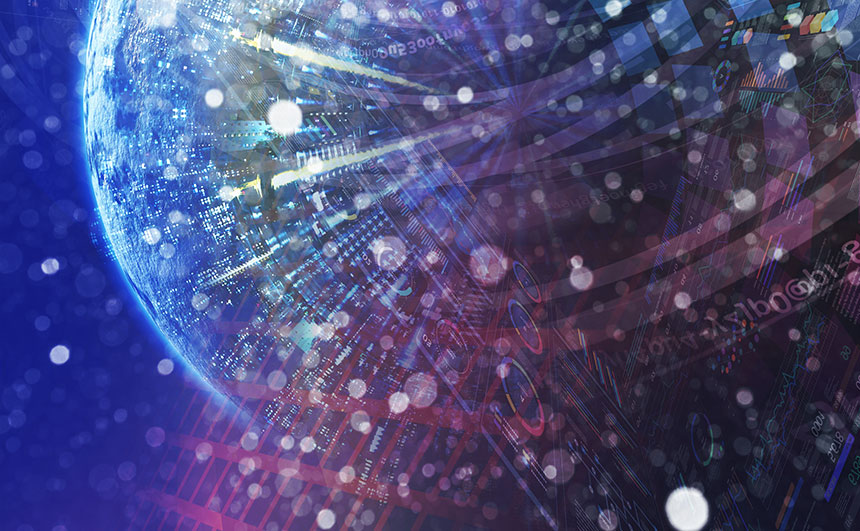
半導体業界においてパーティクル軽減は重要課題です。
しかし高度化するプロセスにおいて、発塵源の特定が年々難しくなってきているという側面があります。
従来、発塵源の特定については、気中パーティクル測定やSEMによるパーティクルの観察を組み合わせることで、どのエリア・箇所から生まれたのか推測する方法がありました。
しかしそれは「発生箇所を推理する」という方式であり完全な特定が難しく、発塵源の特定について行き詰まってしまうこともあるかと思います。
ここでは、従来型のパーティクル計測方法と併せて、「ウエハー表面に留まらない表面付着パーティクルの計測」という新しいパーティクル計測方法を組み合わせることで効率的に発塵源を特定する方法について、解説いたします。
既存のパーティクル計測(発塵源の特定)における課題点
パーティクル低減のためには、3つのプロセスを経ることになります。
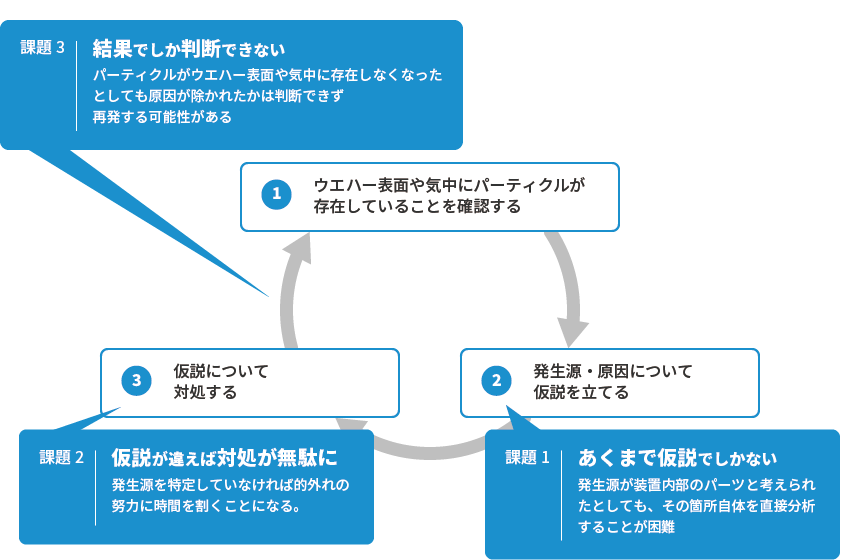
課題1.間接的な測定で導けることはあくまで「仮説」であるということ
例えば、発生源が装置内部のパーツであると推測されたとしても、その箇所自体を直接分析することは困難です。
組み立てられた装置を分解して対象表面を観測しようとしても形状的に難しい場合もあり、かつその分解・再組み立ての過程で条件は変化するでしょう。
従来の方式で気中のパーティクルを測定したり、ウエハー表面に「結果として」付着しているパーティクルを分析することは、あくまで間接的な測定であり、発塵源の特定のための「仮説」と言えます。
課題2.仮説が間違っていれば、無駄な対処に追われます
発塵箇所にあたりを付けてその発生メカニズムを推測し、軽減するための方策を考え実行することになりますが、そもそも仮説が間違っていれば対処が無駄になってしまいます。
それどころか、これまで問題無かった箇所に新たな問題を生じさせる恐れもあります。
課題3.最終結果でしか判断できない
原因箇所を直接測定し特定することができていない場合は、仮説に対して対処してもその結果「パーティクルが減った/増えた/変わらない」ということでしか判断できないことになります。
対処後にパーティクルが軽減されていることを観測したとしても、その対処と現在の状態に対し因果関係が確立しにくい場合もあるでしょう。
つまり、原因が取り除かれたかは判断が難しく、再発する可能性もあります。
もちろん発生しているパーティクルの物質を同定し、プロセス内で使われている部材・材料や化学反応から推測することで発塵源を特定できるケースもありますが、SEM等の高額な設備に加え分析の知見と相応の工数を要し、ハードルは高いと言えます。
そこで、装置内部など気になる箇所の表面を「直接測定」できるツールを組み合わせて用いることを推奨します。
装置内部などの表面付着パーティクルを直接測定してみましょう
Fastmicroは半導体製造プロセスにおける表面付着パーティクルを手軽に行える便利なツールです。
半導体プロセスの微細化より、いっそうのパーティクル軽減が求められている昨今の状況に対し、最新の13.5nmのEUV露光プロセスにおいて採用・活用されているツールとして注目度が高まっています。
使い方としては、パーティクルの発生源の可能性がある箇所に対し、直接サンプラーカードを押し当てて転写させることで付着パーティクルの採取を行ないます。採取したものは数分で自動的に分析され、パーティクルの発生状況を確認することができます。
採取から測定までの流れ
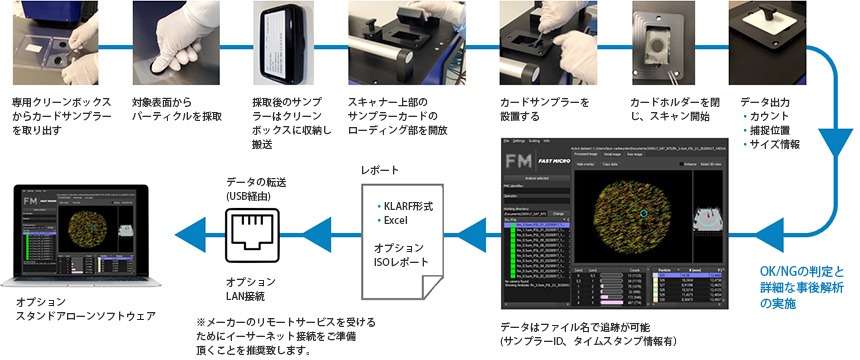
従来型の測定方法とFastmicroを組み合わせて効率的に発塵源の特定を
Fastmicroを用いると、発塵源の特定は以下のように効率化されます。
- 装置やチャンバー内部等、従来型の手法では測定できなかった気になるところをFastmicroで「直接」「すぐに」測定
- 付着パーティクルを観測した箇所について対処する
- 稼働させた後、Fastmicroで再度「直接」測定。その場所のパーティクルが軽減していることを確認。
- 気中パーティクル、ウエハーの表面付着パーティクルの計測によって、パーティクルが軽減されていることを最終的に確認
このように「従来型の測定方法では調べられなかった所を」「直接」「素早く簡単に・何度も気軽に」測定できることがFastmicroの強みと言えます。
発塵源の特定に、Fastmicroを是非ご検討ください。
ご興味を持たれた方はお気軽にお問い合わせください。ご説明いたします。