電子輸送層(正孔輸送層)とは?
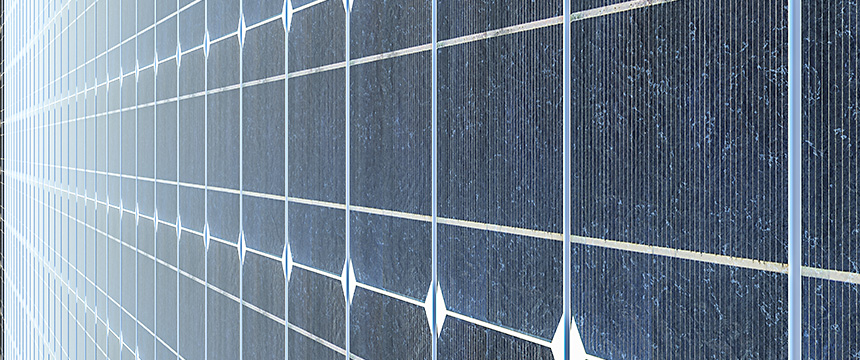
電子輸送層とは、電子を収集し電極(陰極)へと適切に輸送するための膜です。
正孔輸送層(ホール輸送層)とは、正孔(ホール)を収集し電極(陽極)へと適切に輸送するための膜です。
電子輸送層と正孔輸送層は、どちらもペロブスカイト太陽電池を構成する要素の一つです。
収集・輸送を行う対象はそれぞれ異なりますが、役割はよく似ています。
ここでは、ペロブスカイト太陽電池の電子輸送層および正孔輸送層について、製造の方法や課題、有効なソリューションについてご紹介いたします。
ペロブスカイト太陽電池について
ペロブスカイト太陽電池とは、ペロブスカイト結晶構造により発電を行う太陽電池です。
太陽電池には様々な種類があり、構造や製造方法、特徴などが異なります。
従来、太陽電池市場ではシリコン系太陽電池が主流で、建物の屋根や農地など限られた場所で使用されてきました。
一方、ペロブスカイト太陽電池は、太陽電池の活用可能性をさらに広げることができる次世代の太陽電池として注目を集めています。
注目されている理由
カーボンニュートラルの実現に向けて、再生可能エネルギーの活用を広げることが求められます。
ペロブスカイト太陽電池に期待されるメリット・強みには下記が挙げられます。
発電量が多い
太陽光発電として現在使用されているシリコン系太陽電池は、重量と厚みがあるため設置できる場所に限りがあります。
その一方で、ペロブスカイト太陽電池は軽量で薄く、さらに折り曲げることも可能です。
そのため、建物の壁面や携帯型デバイスなど、太陽電池を設置可能な対象が拡大します。
また、ペロブスカイト太陽電池は、曇り空や室内光などの低照度条件でも発電することが可能です。
現在設置されているシリコン系太陽電池を全てペロブスカイト太陽電池に置き換えた場合、発電量が増加することは明白です。
ペロブスカイト太陽電池は現状シリコン系太陽電池と同等レベルの光電変換効率ですが、日々研究開発が進められており、実用に向けてさらなる向上が見込まれます。
製造における将来性が期待できる
ペロブスカイト太陽電池は、製造コストの低さも特長の一つです。
実用・量産に向けて、高い品質を保ちつつ高温処理や真空設備を必要としない、簡易な製造方法の実現が進められています。
また、ペロブスカイト太陽電池の製造に使用されている材料には、日本の化学産業の強みを活かすことができるものが多くあります。
ペロブスカイト太陽電池が量産される社会でも、持続的な材料調達ができる可能性があります。
仕組みと構造
ペロブスカイト太陽電池は、大きく分けると3つの要素を重ねた5つの層で構成されます。
まず中心に存在するのが、発電のコア部分であるペロブスカイト層です。
ペロブスカイト層を挟むように、一方には電子輸送層、もう一方には正孔輸送層があります。
さらにその外側を、電子輸送層側には陰極、正孔輸送層側には陽極の電極で挟みます。
発電の仕組みは、ペロブスカイト層が太陽光を受け、電子と正孔を生成します。
生成された電子は電子輸送層へ、正孔は正孔輸送層へ集められます。
このとき電子輸送層と正孔輸送層は、それぞれ逆の要素が流れ込んでしまうのを防ぐ役割も担います。
電極は、それぞれの輸送層から受け取った電子・正孔を外部回路に供給します。
この一連の流れにより、太陽光が電気エネルギーへと変換されています。
ペロブスカイト太陽電池は、耐久性や光電変換効率などの課題はあるものの、研究開発が進められることで実用化や普及の期待が高まっている存在です。
電子輸送層(正孔輸送層)の製造方法
電子輸送層と正孔輸送層は、どちらも「塗布」により製造されることが一般的です。主にスプレーやスピンコーターなどを使用します。
他にもスパッタリングや真空蒸着を用いた方法もありますが、量産に向けて製造の低コスト化を実現するため、より製造が簡易な塗布を用いた質の高い塗膜形成が採用されています。
製造における電子輸送層と正孔輸送層の差としては、使用する材料の違いがあります。
電子輸送層には酸化チタン (TiO₂)や酸化スズ (SnO₂)が、正孔輸送層には酸化ニッケル (NiO)や硫化銅 (CuS) が多く用いられます。
また、その他の有機材料を使用した研究なども進められており、塗布方法と併せてこれからも検討が続いていくでしょう。
製造における課題
電子輸送層と正孔輸送層の品質は、ペロブスカイト太陽電池の製造に大きく関わります。
そのため、現状ペロブスカイト太陽電池の課題とされている事柄を解決するには、電子輸送層と正孔輸送層の品質向上も有効だと考えられます。
層の均一化が難しい
電子輸送層・正孔輸送層が「均一である」ということは、層を面として見た際にどこを切り取っても同じ厚みで、同じ量の材料粒子が含まれることを示します。
電子輸送層は正孔を、正孔輸送層は電子を、それぞれ電極へ流入しないよう防ぐ役割があります。
層が均一でないことにより、流入を防ぐ役割が発揮できず電子と正孔が結合してしまい、電気エネルギーを発生させることができなくなってしまいます。
そのため層が均一であることは、発電効率の向上に繋がります。
また層の均一化は、電子・正孔の正しい輸送層内部の移動を活性させることでも発電効率の向上に関連します。
しかし、従来のスプレーやスピンコーターでは、膜厚は一定でも粒子レベルで層の均一を実現することが難しく、課題となっています。
適切な膜厚の実現が難しい
発電効率に影響を与える要素には、電子輸送層・正孔輸送層の厚みも挙げられます。
膜が薄すぎると電極への輸送が不十分になってしまい、膜が厚すぎても電化損失の増加に繋がります。
使用する材料にもよりますが、数十~数百nm単位の適切な厚さで塗膜形成が求められます。
薄い塗膜形成にはいくつかの方法が挙げられますが、特に研究開発においては様々な厚みで検証するため、薄い膜を少しずつ塗り重ねることができる方法の選定が有効です。
平坦な表面の形成が難しい
電子輸送層・正孔輸送層の表面の平坦性は、発電効率と耐久性に影響を与えます。
それぞれの輸送層の表面が滑らかであると、ペロブスカイト層との接触が良好になります。
それにより、ペロブスカイト層で発生した電子・正孔を効率よく収集することができるため、発電効率が向上します。
また、ペロブスカイト層と輸送層がしっかりと密着することで、ペロブスカイト太陽電池の劣化原因となる水や空気との接触を減らすことができ、耐久性の向上にも繋がります。
電子輸送層・正孔輸送層の製造に用いられる材料の中には、金属粒子を含むものが多くあります。
そのため、薄膜を形成する過程で表面に粒子の凹凸が発生しやすいことが課題となっています。
電子輸送層(正孔輸送層)の製造に最適なソリューション
電子輸送層・正孔輸送層の製造において、Sono-Tekの超音波スプレーが有効なソリューションとして注目されています。
Sono-Tekの超音波スプレーは、超音波振動により形成された微細な液滴を噴射し、薄い塗膜を形成します。
電子輸送層・正孔輸送層の製造にこの技術を用いることで、下記を実現することができます。
性能の向上
超音波振動により発生する液滴は、非常に小さく、液滴サイズが均一であることが特長です。
この微小かつ大きさの一定な液滴が塗布対象に着弾することで、非常に薄く厚さの均一な膜を作り出します。
また、超音波により均一に形成されるのは液滴のサイズだけではありません。
1つの液滴に含まれる粒子も、超音波振動により均一に分散されます。
そのため形成される膜に含まれる粒子は、石垣のように緻密に並び、表面構造の凹凸を防ぎます。
Sono-Tekの超音波スプレーは、噴射時だけでなく塗布材量を充填するシリンジ内にも超音波振動を与える機構を持っており、粒子の偏りを防ぎます。
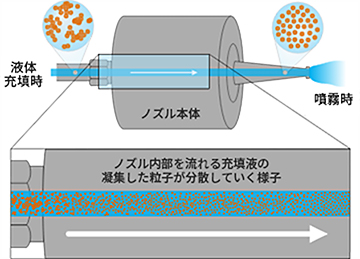
このような特長から、電子輸送層・正孔輸送層の製造にSono-Tekの超音波スプレーを用いることで、発電効率の向上、および耐久性の向上に貢献します。
材料コストの抑制
電子輸送層・正孔輸送層に使用される材料の中には、貴金属などの高価なものも存在します。
非常に薄い塗膜を形成することで材料消費を抑え、コストの低減に繋がります。
ペロブスカイト太陽電池の実用・普及に向けた低コスト化に貢献します。
研究開発の促進
Sono-Tekの超音波スプレーは、幅広いラインナップも特長です。
研究開発向けの小面積塗布に最適のモデルや、大型化に向けた大面積塗布用のモデル、大量生産時に生産ラインへ組み込むためのモデルもございます。
ペロブスカイト太陽電池の実用に向けて、電子輸送層・正孔輸送層の研究開発を加速させます。
電子輸送層・正孔輸送層の製造におけるSono-Tekの超音波スプレー活用について、ぜひお気軽にお問い合わせください。