燃料電池のつくり方
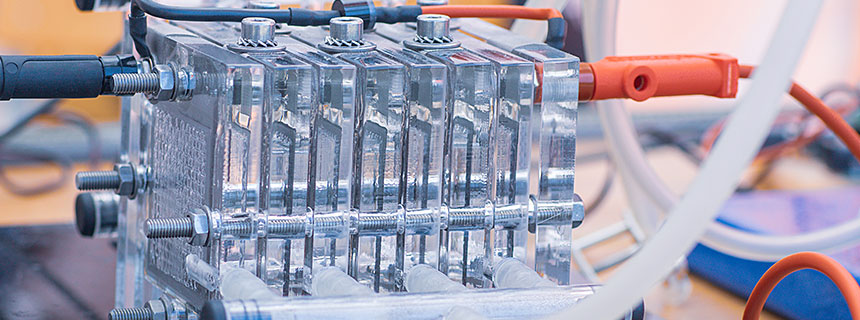
目次
様々な環境問題や地球温暖化の進む中で、クリーンエネルギーとして燃料電池は注目を集めています。そこで、燃料電池の製造に新規参入を検討する企業も増えていると思います。
ここでは燃料電池の基礎的知識から、製造工程、製造における課題など幅広くご説明いたします。
燃料電池の仕組み
燃料電池とは水の電気分解の原理から、水素と酸素の化学反応により電気を発生させる装置です。
燃料電池の原料は水素です。酸素は空気中に21%も含まれているため、空気中の酸素を利用します。
燃料電池の種類
使用する電解質の種類により、主に4種類に分類されます。それぞれ運転温度に大きな差が見られ、それによって活用例も異なります。
燃料電池自体は古くから存在していますが、近年では自動車用や家庭用など、人々の生活に密接な用途に向けて高い安全性を持つ、固体高分子形(PEFC)での研究開発がさかんに進められています。
また、固体高分子型・プロトン膜型(PEM)は触媒に貴金属を使用するという課題がありますが、それに対し触媒が非金属であるアニオン膜型(AEM)も注目を集めています。
方式 | 固体高分子形(PEFC) | リン酸形(PAFC) | 固体酸化物形(SOFC) | 溶融炭酸塩形(MCFC) |
---|---|---|---|---|
解説 | 安全度が高い 最新の方式 |
従来方式 | 従来方式 | 従来方式 |
電解質 | 固体高分子膜 | リン酸 | 安定化ジルコニア | 炭酸塩 |
運転温度 | 70~90℃ | 200℃ | 700~1000℃ | 650~700℃ |
発電効率 | 30~40% | 35~42% | 40~65% | 40~60% |
活用例 | 家庭用、自動車、 携帯機器、ほか |
工業用、発電施設 | 家庭用、発電施設 | 工業用、発電施設 |
研究が進められる中、新しい燃料電池も登場しています。
中でも近年特に注目が集まっているのは、セラミック燃料電池とも呼ばれる、PCFCです。
「PEFCとSOFCの強みを集めた燃料電池」といえる存在です。
基本構造
発電は、燃料電池内部のスタックと呼ばれるシステムで行われます。スタックはセルを積み重ねることで構成され、セルの一つ一つで水素と酸素の化学反応を起こし、発電しています。
セルは平らな板状をしており、電解質を中心にプラス極とマイナス極の電極ではさみ、さらにその両外側をセパレータではさみます。
セパレータの電極に接する側には溝が掘られており、マイナスの電極側を水素が、プラスの電極側を酸素が通ります。さらに電解質と電極の間には触媒が塗布されており、それらによって反応が起こり電気が発生します。
燃料電池の製造工程
発電のコアとなるスタックの製造工程をご説明いたします。
セパレータ
セルをスタック化する際に、水素が通るセパレータと酸素が通るセパレータが、裏面合わせに積み重ねられます。そのため2体のセパレータを一体化し、バイポーラプレート(BPP)として製造されることが一般的です。
BPPは用途によってカーボンまたは金属を材料として用います。カーボンの際は圧縮成型、金属の際はプレス成型によって製造されます。
MEA
MEAとはGDL(電極)で挟んだ電解質と、その間に触媒が塗布されたものを指します。
固体高分子形燃料電池(PEFC)では、MEAの中心にある電解質をPEM(プロトン交換膜)と呼びます。
触媒の塗布にはCCMとGDEという形式があり、触媒をPEMに塗布するか、GDLに塗布するかによって異なります。

MEA製造過程で使用される材料は白金など高価なものが多く、製造精度の高さと材料ロスの低減が重要です。
電解質と電極はそれぞれ板状であり、触媒をそれらに塗布・乾燥します。触媒の塗布方法は様々ですが、ここでは5種類ご紹介いたします。
ダイコーター
対象物に対し、スリットダイから塗布材を押し出しながら動かすことで塗膜を形成する装置です。比較的生産性が高い一方で、異方性を持ってしまうこと等が燃料電池製造においてはデメリットとして挙げられます。
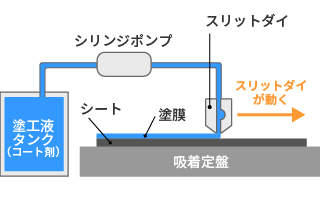
スクリーン印刷
孔版印刷の一種で、印刷したい部分のみ塗布材が通過するよう版を加工します。対象物に版を重ね、その上から塗布材を塗り広げることで塗膜を形成します。必要な部分にのみ塗膜形成をすることができます。しかし近年ではより薄い塗膜の形成が求められており、その他の方法が採用されることが多くなりました。
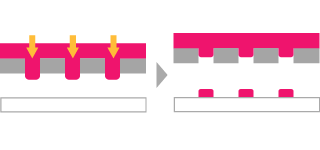
エアスプレー
塗布材を空気や圧力によって霧化し、対象物に吹き付けることで塗膜形成を行います。オーバースプレー(塗布材が対象物を外れて飛散すること)や跳ね返りによる材料ロスが懸念されており、その他の方法に比べて燃料電池の製造に使用されることは少ないといえます。
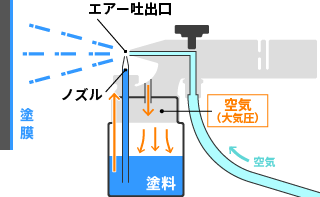
静電スプレー
静電気によって液滴を形成し、対象物に塗布を行います。しかし燃料電池製造においては、広範囲の塗布が難しく生産性に懸念があること、塗布材の乾燥や液詰まりの発生、触媒に含まれる白金などの金属粒子が偏り発生という難点があります。
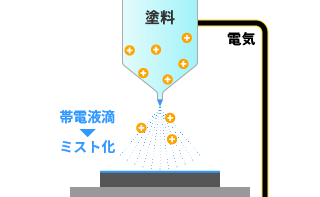
超音波スプレー
スプレー先端から出た塗布材が、超音波振動により小さく均一な液滴となり、対象物に塗布されます。目的・用途に応じて、超音波の周波数やノズルなどを使い分けることが可能です。
非常に薄い塗膜形成が特長で、材料ロスを低減します。また塗布材に圧力や電力をかけないため、粒子の偏りも防ぐことからお勧めの塗布方式です。
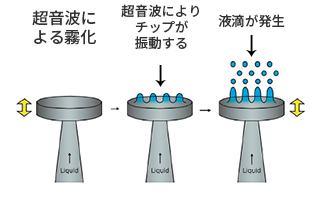
セル、スタック化
そうしてできたセパレータとMEAを交互に積層し、多数のセルを重ねることでスタック化されます。
その後エージング試験やテストを行い、実用可能と判断されたものがシステム部品として使用されます。
燃料電池の製造の課題
PEFCでのMEA製造方法は確立されつつありますが、今後の水素社会での大量消費に対応すべく、量産に向けて研究開発を重ねる必要があります。特に主要なクリアすべき課題とされている点について解説いたします。
コスト、材料の削減
燃料電池を構成する材料は高価なものが多いです。そのため製造過程における触媒材料ロスの削減や、より少ない触媒材料で高い性能を発揮する製造法などの研究開発が進められています。
製造の高速化
今後実用化の進む燃料電池の量産に向けて、MEA製造の更なる高速化が求められます。
研究開発から量産までを見据えたシームレスに展開できる製造設備が必要です。
発電効率や製品精度の向上
コストや各プロセスにおける製造時間の削減を行う際、同時に製品の精度を保つ必要があります。
発電効率は高く維持する必要があり、また性能にばらつきがないことなどが求められます。
触媒の塗布工程において有効なソリューション
このような課題に対し研究開発が進められており、既に実用化されているものも増えています。
その中でも弊社のご提案するSono-Tekの超音波スプレーは、MEA製造の触媒塗布の工程において、触媒消費量の低減及び発電効率の向上に繋がるソリューションとして有効性をご確認いただき、多く採用されています。
また近年、触媒の厚みに傾斜構造を付与することで性能が向上するという研究成果も発表されています。
従来の方法ではこれらを実現するのは困難とされていましたが、超音波振動によって霧化した触媒は、非常に薄く緻密な塗膜を形成します。さらに局所的な塗布も可能なため、傾斜構造も実現します。
超音波スプレー製品は、研究開発用の小型のものから、量産に対応できるモデルまで取り揃えており、研究開発からプロダクションへシームレスに展開が可能です。