動画でわかるインクジェットヘッドの最適な駆動波形の見つけ方
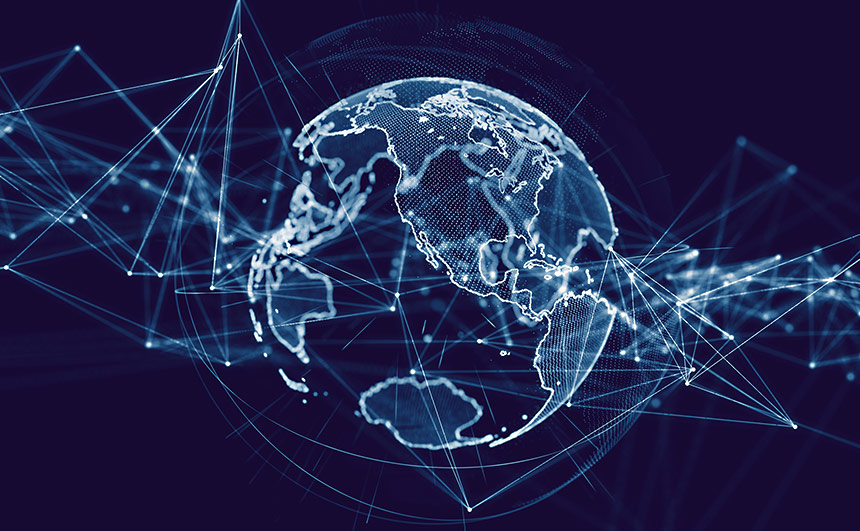
産業用インクジェットヘッドを用いた研究開発において、駆動波形の最適化は重要です。
本項では駆動波形の最適化を行なう方法について動画でご案内いたします。
なぜ駆動波形の最適化が必要か?
産業用インクジェットヘッドは、ファンクションジェネレーターにより生成された電気信号を元に駆動します。
電圧が高いとき/電圧が低いときにどう駆動するかはメーカーにより方式が異なるため、一律ではありません。
そもそも波形とは何か(基礎解説)
駆動波形の最適化が必要な理由
通常のインクであればメーカーが指定する推奨波形で良いのですが、ユーザーの要求次第によっては、ご要望のインクに適した波形に変えることがあります。
また、要求の厳しいアプリケーションの場合、システムのあらゆる面を最適化する必要があります。
その場合、ちょっとインクが出たというくらいではダメで、完璧な吐出を達成しなければなりません。
そのために行なうことが、駆動波形の改善(最適化)です。
駆動波形の最適化で取り組むテーマ
駆動波形を変えることで、結果として下記のような変化が起こります。
- 液滴の体積変化
- 飛翔速度の変化
- サテライト滴のサイズと数の変化
- 吐出挙動全般の安定性の変化
これらを最適化することで、目的とするアプリケーションに適合したインクジェット吐出達成を目指します。
駆動波形の最適化で調整するパラメータ
- パルスの電圧
- パルス幅(電圧のホールドタイム)
- 電圧の印加時間
これらを調整します。
波形最適化はゴールを決めることが大切
ゴールはアプリケーションによって異なります。
あるアプリケーションにおいて「良い」とされる吐出結果が、別のアプリケーションでは「不適」となり得ます。
例えば、サテライト滴が形成されることが良いことなのか、悪いことなのか、それは一概には言えません。
用途・条件によってはサテライト滴が発生しても良いケースもあるためです。
意外とサテライト滴がある方が印刷が安定しているケースもあります。
また、液滴の飛翔速度も考慮すべき要素です。
ある用途ではより高速な液滴が望まれ、ある程度のサテライト滴は許容されます。
例えば布地に印刷するテキスタイルプリント等ではインク液滴をかなり遠くまで飛ばす必要があります。
つまり、ヘッドとメディア間の距離(ヘッドギャップ)を大きく取る傾向があり、高速な液滴が望まれます。
対して、プリンテッドエレクトロニクスのような高精度用途は逆で、ヘッドギャップは非常に小さくなります。
想定していない余分な箇所に導電性の液滴が飛び散っていないことの方が大事です。
波形最適化の5つの基準
では、駆動波形の最適化にあたり、どこに着目すれば良いのでしょうか?
具体的に下記5つの基準を基本として提示します。
- サテライトの数と量、どこまで許容されるか?
- 液滴の量(体積)
- 液滴の速度
- ヘッドギャップの距離(どれだけ離れると問題になるのか)
- 速度、周波数、解像度の関係
最適な答えは最初はわかりません。ある程度印刷してみる必要があります。
そこで、駆動波形の操作~吐出状態の観測~印刷までを一続きのものとして行えるシステムがImageXpert社から提供されているjetXpertです。
これを使ってどのように最適化を進めるのか見ていきましょう。
駆動波形最適化の例
準備.始めに、ヘッドメーカーが推奨するシングルパルス波形を試してみます。
このシステム(jetXpert)は、メジャーな産業用インクジェットヘッドメーカーであればいずれも駆動させることができるマルチベンダー対応のシステムです。
それを実現するのが、搭載されているGIS社の駆動回路です。
産業用インクジェットヘッドの世界では、駆動回路を各ヘッドメーカー/デバイスメーカーが開発するコストを省くために、駆動回路を開発している専業ベンダーがあり、その最大手の一角がGIS社です。
GIS社の駆動回路を用いてjetXpertで研究開発したものは、そのままGIS社の駆動回路を製品に搭載することで製品化が可能です。
さて、jetXpertに搭載されたこのGIS社の駆動回路を用いて、駆動波形の最適化を行なってみます。
このシステムが優れている点として、ソフトウェアを介して波形最適化のためのパラメータを変更できるということが挙げられます。
例えばテストしたい電圧のリストを作成して、GIS社の駆動回路に自動送信することが可能です。
すると吐出を止めず、自動的に駆動波形の電圧が変更され、液滴観測を行います。
STEP1.サテライトが少なくなる電圧を探す
各ソフトウェアが駆動回路と液滴観測装置を制御しており、駆動波形のセット~吐出~撮影を、電圧を変えながら繰返します。
ソフトウェアにより電圧を変えて自動でテスト可能な点が、このシステムの優れた点の一つです。
波形の電圧を上下させて、液滴の速度とサテライトの数のバランスを実験します。
撮影された画像を見ると、右端では吐出後4つ程のサテライトが生じていることが観測できます。
電圧を変えると速度が変わります。
実際に各速度で印刷してみます。
エッジ、インクのにじみ具合、印刷媒体上でのサテライトの有無(=ドットの形状比較)を確認します。
ヘッドギャップや印刷媒体の搬送速度は用途毎に独自の条件があり、それら条件が液滴速度と形状の適切なバランスを決める上での助けになります。
ここで、どこまでサテライトが許容されるか、どの程度の速度が良い結果を得られるのかについてはアプリケーションの特性を考えつつ整理しておきましょう。
ここでは、サテライトの少ない見栄えの良い液滴を吐出できる電圧値をセットした状態で、次のステップに進むことにします。
STEP2.最適なパルス幅を探す
液滴体積と吐出速度を最大化するパルス幅を探してみます。
ピエゾインクジェットヘッドの仕組みとして、電圧を印加すると振動版が動き、インク室に圧力をかけ、液滴が吐出されます。その際インクは下に圧力がかけられ、反射して上に戻ります。
理想的なパルス幅は、この圧力が掛かっている方向とインクが進む方向が常に一緒の状態です。
なぜなら、パルス幅が適切でなければ、インクが反射して戻ってきている最中に、次の周期の印加が行われ加圧されるので、圧力とインクの戻りが衝突してインクの挙動が乱れるためです。
理想的な挙動は、リズミカルにインクが動くことであり、そのための適切な「パルス幅」を見つける必要があります。
振動版からの圧力の方向とインクが進む方向が完全に同期しているとき、液滴吐出速度は最大となり、このときのパルス幅が最適解と言えます。
このサンプルケースでは2.1~2.2マイクロ秒が最適でした。
STEP3.パルス幅を固定してパルス(電圧)の高さを調整する
ここまでの取組みで、理想的なパルス幅が把握できました。
ではこの最適化されたパルス幅を固定して、電圧を上下に振ってテストしてみます。
どこまでサテライトが許容されるか、どの程度の速度が良い結果を得られるのかは、事前にSTEP1でまとめられている前提で、もしスピードが速くサテライトが無い方が良いなら、それに適した電圧を選びます。
STEP4.印刷速度を変えても問題無く機能するか確認する
プリンターメーカー、インクメーカー共に、印刷速度が速くても遅くても良い結果が得られることを期待します。
そのため、多くの異なる周波数でテストすることが必要です。
引き続きGISの回路を用いて吐出周波数を変更しテストしましょう。
左端:吐出周波数1kHz、右端:吐出周波数30kHz
ポイントは、「周波数を変えても吐出速度が一定か」「サテライトは無いか」「吐出破綻や、不吐出がないか」を見ていきます。
もしうまくいかない場合は、前のステップに戻り電圧を少しだけ下げてみると良いでしょう。
複数パルスの組み合わせを検討する
ここまで紹介してきたケースでは、シンプルなシングルパルスでした。
しかし、例えば階調印刷を行なう場合、複数の異なるサイズの液滴を形成する必要があります。
また、液適量や速度が不十分な場合でも複数パルスを検討する必要が出てきます。
最適化したパルスを複製し、パルス同士の間隔を調整します。

液滴の量と速度が最大となるようなパルス間隔を見つけます。
インクジェット業界では「プリントヘッドの音響時間(共振時間)を決めようとしている」と表現します。
インクがノズル内の前後を往復して動き、ノズル内で反射して戻ってくる時間のことです。
この時間がどれくらい掛かるかによって、複数のパルス間隔を正確に決めることができます。